
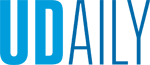

Making moon rocks
Photos courtesy of Team 116 and NASA May 21, 2024
UD mechanical engineering students help NASA test a moon rover
As aspirations for lunar colonization grow, so does the need to understand the moon's freshwater reservoirs. Researchers are interested in determining if these hidden natural resources could serve as a source of drinking water and as fuel, both of which are key cornerstones for any long-term lunar habitat.
To this end, NASA is investigating new areas of the moon for signs of freshwater. As part of this effort, the Volatiles Investigating Polar Exploration Rover, or VIPER, aims to characterize the distribution and physical state of lunar waters and then to determine whether humans will be able to use lunar water resources found on the moon.
But before VIPER launches in late 2024, a number of tests must be conducted here on Earth to ensure that the golf cart-sized rover can withstand harsh lunar conditions. This is what a team of seniors in the University of Delaware’s College of Engineering worked on as part of a project that could aid in mankind’s next giant leap.
How to make a moon rock
Senior Design “Team 116” includes Hannah Epstein, Matt LeCates, Kenny Madden, Matthew Ongtawco and Xavier Stephenson, all of whom are mechanical engineering majors, working under the supervision of associate professor Joseph Feser along with NASA lab manager and UD mechanical engineering alumna Erin Rezich.
The students were brought together as part of the Interdisciplinary Senior Design program, a hallmark of the senior year for UD’s mechanical and biomedical engineering programs. Through this program, student teams work with industry sponsors and faculty advisors to design, build and test a solution for a potential product or an ongoing research project.
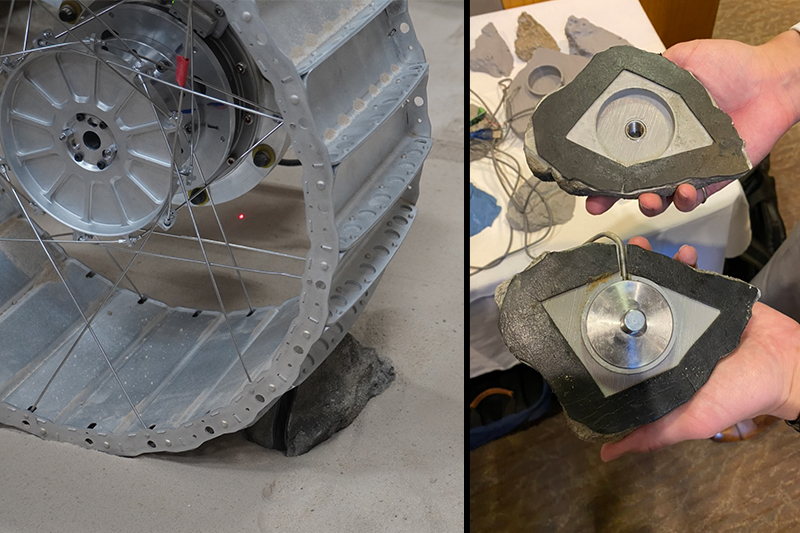
For their senior design project, the group was tasked by the NASA Glenn Research Center and the Delaware Space Grant Consortium to create synthetic moon rocks that would be used to test whether the VIPER rover could withstand the harsh terrain of the lunar surface.
These synthetic rocks needed to both match the material properties of lunar highland rocks while also containing sensors that could deliver data on the force being applied to help understand how the rover is maneuvering over the rocky surface. Team 116 also needed to develop a rock manufacturing process that could easily be replicated to ensure that similar synthetic moon rocks could be produced for future experiments.
“Something like this hadn’t been done before,” Ongtawco said. “There's a phase in the designing process where we do background research on what we think we might need and benchmarking on things that already exist so that we don't have to reinvent the wheel and we found that there was no background research or any background experiments on this rock.”
“This team initially faced a wide variety of engineering design challenges spanning from materials science to data science to manufacturing to instrumentation design and even mundane worries like how to sand-proof scientific measurements,” Feser said. “But the students all had a proactive mindset and divided the project into manageable chunks that they were able to chip away at until they were able to design, build, and test a prototype.”
Over the course of 16 weeks, the group defined, conceptualized, designed and tested their synthetic moon rocks. While there was no blueprint on how to make a moon rock, Team 116 was able to find information on the material properties of lunar rock samples, sensor technology and synthetic rock manufacturing processes. It was through trial and error that the team refined each detail of the design and created their prototype.
“We went step by step, thought of multiple different solutions, found which solution worked the best and basically drew our own path into finding the best solution,” Ongtawco said.

Their resulting synthetic moon rock includes a 3D-printed outer layer made from polylactic acid (PLA) filament that is coated in concrete. 3D modeling is advantageous because it is easy to replicate, while the PLA filament is a lightweight material that simulates the effects of lunar gravity, which is one-sixth of that of Earth’s.
Inside of the rock, a threaded load cell sensor is mounted, and each rock can open and close through a sliding mechanism to access the sensor. A foam gasket provides a seal against simulated lunar sediment to prevent sensor reading interference, and data is collected using a signal amplifier; Stephenson wrote code that transformed the sensor output data into a force reading.
During the Interdisciplinary Senior Engineering Design showcase, where students present their findings to their project sponsor, Team 116 said that while their findings showed that the synthetic rock's size, weight, deformation and hardness were in line with lunar rock parameters, there was still work required in order to get accurate enough force measurements.
Going to Glenn
Not to be deterred, Team 116 took their synthetic rocks to NASA’s Glenn Research Center to continue refining and perfecting their prototype. From Jan. 10-13, Team 116 worked alongside aerospace engineers in the Simulated Lunar Operations Laboratory (SLOPE), where they were able to gain new insights on the impact of their senior design project.
“Working in that environment, being in the SLOPE lab, getting to pick the brains of people who do it for a living, really helped all of us understand the capabilities of what we were working on,” Epstein said.
Having completed developing the synthetic moon rocks, the research center had a new project ready for Team 116: measuring NASA’s airless flexible tires’ contact footprint, or the portion of the tires that are in contact with the lunar/planetary surface. These new tires are made from metal mesh and outfitted for cutting-edge rovers. They have the benefits of being low maintenance and less expensive to produce while still being dynamic and flexible enough to roam the rocky wastelands of the moon. But, like other innovations at NASA, the airless tires need to be tested before they can be used.
As a continuation of their senior design capstone project, Team 116 is now creating a product for the SLOPE lab that can measure the pressure distribution of these tires on the contact surface while also assessing the deformation and buckling of the tire itself.
Building friendships
While it was luck that Epstein, LeCates, Madden, Ongtawco and Stephenson were placed on the same team, it was their common interest and shared passion for this project that enabled them to create an amazing team.
Thanks to their excellent project management skills, strong work ethic and ability to foster a working environment founded on mutual respect, the five seniors have been able to develop multiple projects for one of the most well-known space agencies in the world.
The team spent a lot of time together during the trial-and-error phase of the moon rocks development, an experience that also helped them become friends. When asked about the best part of this incredible project, Team 116 unanimously agreed that it was working on this project together.
“The best part was definitely spending time with these people and having intelligent, creative, kind and fun people working together on a tough project,” Madden said.
Contact Us
Have a UDaily story idea?
Contact us at ocm@udel.edu
Members of the press
Contact us at 302-831-NEWS or visit the Media Relations website