
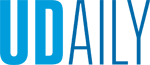
Wearable tech assesses performance of prosthetic leg usage: youtube.com/watch?v=ECG8K5AFyQ8
Revolutionizing prosthetics
Photos and video by Ashley Barnas Larrimore July 22, 2024
UD research aims to improve the lives of those with limb loss
John Horne lost his right leg to bone cancer when he was a freshman in high school. This intensely personal experience spawned his career and passion for advocating for those with limb loss. The president of Independence Prosthetics-Orthotics on the University of Delaware’s Science, Technology, and Advanced Research (STAR) Campus has seen prosthetics improve significantly since his limb loss and since he was an undergraduate student at UD, interning at Nemours Children’s Health, where he poured prosthetic molds.
Now, Horne is part of pioneering research led by George W. Laird Professor of Mechanical Engineering Jill Higginson in the Neuromuscular Biomechanics Laboratory along with co-investigators Elisa Arch, associate professor of kinesiology and applied physiology, and Meg Sions, associate professor of physical therapy, in the College of Health Sciences. The study aims to test the potential of fabric-based sensors in monitoring load in individuals with limb loss, a development that could revolutionize the field of prosthetics and significantly improve the lives of those with limb loss.
“By monitoring limb loads in individuals with lower limb amputation, we can determine whether they’re loading symmetrically or overloading over time to ensure they’re using their limb optimally,” Higginson said.
These innovative sensors were developed by Erik Thostenson, professor of mechanical engineering in the College of Engineering; Sagar Doshi, an associate scientist in UD’s Center for Composite Materials; and Higginson.
Horne first experienced force-sensing devices in an orthopedic boot for people with Achilles tendon rupture as part of a senior design project in Higginson’s lab several years ago and identified an unmet need in the limb loss community.
“The difference between the socket and the foot in a prosthetic pylon is an area that functionally we haven’t taken advantage of until now,” Horne said.
Horne demonstrated that the ongoing study requires placing the small sensors in the pylon of his prosthetic. He then walked on a treadmill with force plates in the motion capture lab to gauge whether the treadmill data mirrored the sensor data.

“Wearable technology like these sensors can help us monitor loads and gauge performance in the real world,” explained Higginson.
Those implications are significant for people with limb loss.
“The conversation, clinically with patients, has always been tough to translate what the patient is feeling,” Horne said. “A device like this gives us hardcore data so clinicians can directly understand what’s happening and make changes.”
It could also help patients who lack access to healthcare.
“The device could generate data from patients in rural areas who may be having prosthetic issues, and we can adjust without them being onsite,” Horne said.
Higginson’s research is made possible with vital support from the Maggie E. Neumann Health Sciences Research Fund. Their generous contribution has been instrumental in bringing this research from the lab into the real world, where it can make a tangible difference.
“When you’re working with a special population, a potentially vulnerable population, pilot data is necessary, and obtaining that initial funding from Maggie E. Neumann Health Sciences Research Fund has been instrumental in helping us validate whether the system is working properly,” Higginson said. “It also sets the stage for funding opportunities from the National Institutes of Health or the National Science Foundation for larger studies.”
A collaborator from the beginning
Hanna Armstrong, an honors student, graduated from UD in May with her bachelor’s degree in biomedical engineering and has worked in Higginson’s lab since high school. As a student at Aberdeen High School in Maryland, she attended National Biomechanics Day on STAR Campus and was fascinated by what she saw.
“I learned medicine and engineering co-exist and that together we can find creative solutions to health challenges, and that motivates me,” Armstrong said. “This study has been the holy grail of all the work and lessons I’ve acquired thus far. Thanks to the Neumann funding, we’ve pulled all the resources we needed to complete data collection. Working with patients and learning about their experience and excitement for the device has been a great experience.”
Armstrong, who sorted through the data, said, so far, it’s working.
“Right now, the only time we know if something is wrong with a person’s prosthetic is when they’re in pain,” Armstrong said. “These pressure sensors stand to change what rehabilitation looks like for people with limb loss.”
Working in Higginson’s lab has prepared Armstrong for the next step in her career as she pursues her doctorate in biomedical engineering.
“As an undergraduate student, I’ve been able to work on a project from the beginning and experience the growing pains of research and failure,” Armstrong said. “Learning that every mistake isn’t the end of the world has taught me the importance of resilience and persistence when problem-solving. Learning these lessons early in my career has prepared me to go from undergraduate directly into a Ph.D. program.”
Theophilus Annan, a first-year student in the biomedical engineering doctorate program, will now take over the project.
“Seeing the progress through the years has been incredible,” Annan said. “I’m excited to be part of this novel study and motivated, as an engineer, to find a solution to a clinical problem that could improve the lives of individuals with limb loss.”
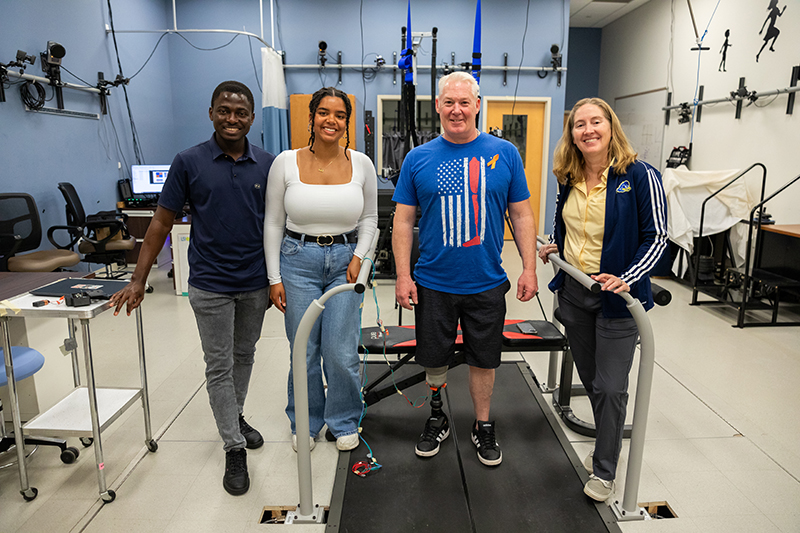
Next steps
Once the pilot study is complete, Higginson, who also directs UD’s new Institute for Engineering Driven Health, sees two natural paths forward: one more industrial-focused and another more clinically oriented.
A clinical trial will better gauge the sensors' effectiveness as a tool for determining load, which is critical to gaining insurance acceptance of the solution.
That piece influences the commercialization piece.
“The Institute for Engineering Driven Health has a mission to translate medical technologies like these sensors from the lab into practice,” Higginson said. “Together, we’ll work with the Office of Economic Innovation and Partnership to make it easier for inventors to take a device with clinical utility and make it more accessible.”
However, the wearable technology has implications that extend far beyond the amputee population. Higginson envisions the tech being used by elite athletes.
“These sensors could determine whether a figure skater is using the right push-off force for various jumps or whether golfers are loading their limbs properly during their swing,” she said.
These kinds of practical implications drive Higginson.
“This is why we do this,” Higginson said. “As engineers, pivoting and applying our skills to address novel problems drew me to this field, and impacting human health remains my primary goal.”
About the Fund
Maggie E. Neumann Health Sciences Research Fund was established in 2020 to support research designed to improve health and quality of life outcomes for children and adults with physical and developmental disabilities. While the fund resides at the College of Health Sciences, the intent is to support interdisciplinary research across all UD colleges.
The research fund was created with a gift from Donald J. Puglisi and Marichu C. Valencia in honor of their granddaughter, Maggie E. Neumann. Puglisi is a member of UD’s Board of Trustees, and they both serve on the President’s Leadership Council.
Contact Us
Have a UDaily story idea?
Contact us at ocm@udel.edu
Members of the press
Contact us at 302-831-NEWS or visit the Media Relations website