
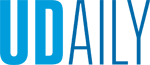

Improving materials design
Graphic illustration by Jeffrey C. Chase November 08, 2023
Fundamental model can help researchers understand how things work
Toothpaste has a hard job. Not only does it have to perform essential functions like scrubbing that coffee residue from your pearly whites, but it also must stay in the tube, exit smoothly under pressure and balance on a bunch of bristles without running all over the bathroom sink.
And every user, everywhere, appreciates it when any excess paste extruded, but not needed on the toothbrush, slides seamlessly back into the tube.
This is an example of a thixotropic elastoplastic suspension made from many different particles. Now that’s a mouthful.
According to Norman Wagner, Unidel Robert L. Pigford Chair in Chemical and Biomolecular Engineering at the University of Delaware, these types of suspensions are found in everything from lotions to 3D-printing inks to building block materials for items, including rubber tires, clays, cements and more.
Many of these materials are made through experimentation — trial and error. Your tire material doesn’t have enough shock absorption? Mix up a new batch of particles to reduce the bounce.
Wagner and a team of UD researchers wondered if there was a way to start from a fundamental picture of the particles and their interactions on the front end, that could be controlled through the chemistry, to develop an end-product with the desired material properties.
The result is a foundational model with applications for understanding a variety of materials, including human blood flow, consumer products like plastics, or carbon black and silica dispersions found in industrial products for manufacturing tires to semiconductors.
The research team’s approach, funded by the National Science Foundation, was recently featured on the cover of AIChE J, the flagship journal of chemical engineering.
As engineers across the country converge in Orlando, Florida, this week for the 2023 AIChE annual meeting, held Nov. 5-10, UDaily talked with Wagner about the work.
Q: What is the problem you were trying to solve?
Wagner: Things like toothpaste, cements, geopolymers — even common household products like your plastic laundry detergent bottle — are composed of many particles that combine or break apart under different conditions. In toothpaste, there are particles for cleaning, freshening your breath and making sure the toothpaste foams. Particles in plastics like a laundry detergent bottle give the bottle its color.
This paper addresses a new approach that we've been developing in our group to start from a fundamental picture of the particles and their interactions to connect the dots between the material’s structure, how that's affected by the processing flow and how it leads to a final material’s properties. In theory, this would allow us to start with a fundamental description, which you can control through the chemistry, and then develop an end-product that gives you the desired material properties. The model is based on population-balance modeling, a very powerful tool used in chemical engineering, as well as other disciplines. For example, my research group used this tool during the pandemic to model how behavior could influence coronavirus (COVID-19) transmission in the UD community.
Q: Why would nonscientists care about this research?
Wagner: This could be ensuring that toothpaste stays on the toothbrush or that ketchup stays on the hot dog without making a mess. That's trivial. But take a solar panel, where there are connections that are made through silver particles in a paste. Here you want to essentially screen print a slurry of silver particles and then fuse those silver particles to make the wires. Now, if you can improve that, you'll make solar panels that last longer, but that wire also covers some of the panels that could be collecting solar energy. So, a possible application where this type of modeling is very important are industrial processes like printing, because if we can make the wires better, narrower or more uniform, through understanding how to better formulate the paste to get the printing we want, we might be able to improve a solar panel’s efficiency by a few percent. Multiply that few percent by an infinite number of solar panels, and that's a big number. So, where you want better products, tougher plastics, better automotive things, the ability to 3D-print filled systems like ceramics, metals or cement, you need a better control of the material’s flow behaviors and final properties.
Q: How does this relate to blood flow?
Wagner: Blood flow is interesting. Blood cells are particles. In your body, red blood cells come together, and they stack like coins. These stacks form aggregates of particles that are important for how blood flows through the body, your heart and arteries, for example. We need blood cells to aggregate for things like clotting, but we don't want them to aggregate in the wrong place at the wrong time. So, it's important to model this correctly for use cases, such as health care devices or other applications.
Q: Why is it a big deal to have your work featured on the cover of AIChE J?
Wagner: For chemical engineering, this is the flagship journal of our discipline. That’s special. It's a fundamentally new approach. People have done population-balance modeling and modeled these types of fluids empirically for a long time. But people haven't really made the connection in a way that is a basis for further work in the future. We did the theory. We have the experimental data that helped validate this foundational science, and there are clear applications to many industrial problems where it might be worth trying this approach.
Q: What about the human side of the work?
Wagner: It’s interesting to think about the people involved — particularly the students and where they ended up after this work. For example, Soham Jarawal, who did the modeling work and based his doctoral thesis on this project, is now at W.L. Gore doing blood flow modeling. Julie Hipp, a former graduate student, performed award-winning neutron scattering work to measure these particle distributions and sizes under flow in carbon black that helped validate this new theory. Today she is employed by Procter and Gamble. Then there’s Rong Song, who spent time working with Chemours on titanium-dioxide particle technology while completing her master’s degree at UD.
This work is a beautiful example of how different expertise and collaborations come together to do something foundational that can be used to improve materials found everywhere from health care to industry to consumer products and processes. It’s also a lens into the places these collaborators take what they’ve learned, their education and experiences, and grow in new directions outside of UD.
Contact Us
Have a UDaily story idea?
Contact us at ocm@udel.edu
Members of the press
Contact us at 302-831-NEWS or visit the Media Relations website