
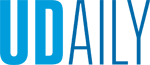

Sustainable manufacturing
Illustration by Jeffrey C. Chase January 10, 2022
UD and LSU collaborate to advance manufacturing technologies that employ carbon dioxide and renewable energy
Reducing the world’s reliance on petroleum and natural gas is a worthy goal, one that could help us achieve a smaller carbon footprint. It will, however, mean rethinking how we create many of the products in our everyday lives.
Chemical manufacturing, the practice of taking raw materials and turning them into products using chemical processes, is an $800 billion industry that supports over 6 million jobs in the United States each year. It contributes to the production of everything from food, buildings and clothing to items found in industries such as health care, electronics and transportation.
Traditional chemical manufacturing relies on non-renewable fossil energy sources for power and raw materials. A more sustainable option gaining steam is the use of electrolyzers, devices that instead use electricity to convert raw materials like carbon dioxide (CO2) into useful molecules for chemicals and products.
One hurdle that keeps promising CO2 electrolyzer technologies in academic laboratories rather than being scaled for industrial use — where they could make a dent in our carbon dioxide emission problem — is that the critical materials needed for the job, including membranes and catalysts, aren’t yet durable or efficient enough to operate over long periods of time.
University of Delaware engineers Feng Jiao, Yushan Yan and Koffi Pierre Yao and colleagues at Louisiana State University (LSU) are collaborating to overcome these challenges.
The work is funded through a $4 million grant from the National Science Foundation’s Established Program to Stimulate Competitive Research (NSF EPSCoR) program. A total $1.9 million of the funding was awarded directly to UD.
Collaborators from LSU include John Flake, the project principal investigator and chair of the LSU Cain Department of Chemical Engineering; Kevin McPeak, associate professor of chemical engineering; Orhan Kizilkaya, assistant professor at the LSU Center for Advanced Microstructures and Devices; Noemie Elgirishi, assistant professor of chemistry; and Phil Sprunger, professor of physics.
Tackling technical challenges
A main goal of the collaborative project is to co-develop an efficient CO2 electrolyzer that can produce ethylene, a widely used chemical building block found in everything from plastics to PVC pipes, textiles to tires.
To begin, the research teams must first understand what affects the system’s durability. One of the key components that impacts the overall performance of electolyzer devices is the polymer membrane, which separates the two electrodes (the cathode and the anode) and functions as an ion conductor, ferrying electrical charges across the system.
Current membrane materials are not built to withstand the harsh conditions found in CO2 electrolysis devices. At UD, Yan, the Henry B. du Pont Chair in Chemical and Biomolecular Engineering, will lead a team focused on making these membrane materials chemical resistant, strong and mechanically robust so that they can last longer — years instead of months.
“I have a basic understanding of how membranes work, but I need a true membrane expert like Yushan to make the membrane stronger and more efficient for CO2 electrolyzers,” said Jiao, Robert Grasselli Development Professor of Chemical and Biomolecular Engineering, who is coordinating the UD side of the work.
A member of the National Academy of Inventors, Yan is a leading expert in developing membranes for electrochemical devices, such as eco-friendly fuel cells and electrolyzers for creating clean energy from hydrogen and carbon dioxide. He also brings experience bridging fundamental and applied research to advance solutions to the marketplace, having launched a UD spinoff to commercialize promising technology for producing sustainable green hydrogen.
Meanwhile, Jiao has been working on electrolyzer technologies for nearly a decade. Most recently, his research team developed a novel two-step process that improved the selectivity and efficiency of carbon dioxide (CO2) electrolysis for creating multi-carbon products. He also co-founded a startup company called Lectrolyst that focuses on ways to convert carbon dioxide into molecules for high-value specialty chemicals. This background will come in handy as Jiao leads UD efforts to engineer catalysts that will allow the UD/LSU device to operate at peak performance.
And Yao, assistant professor of mechanical engineering, will help the UD and LSU teams better understand and engineer the boundary between the catalyst and membrane within the electolyzer system itself and examine the potential of catalysts, such as silver and copper, to deliver desirable and achievable properties.
Early this year, an LSU graduate student will visit UD to learn how Jiao builds his carbon dioxide electrolyzer and bring this knowledge back to the LSU team, which is developing its own system. Jiao said this type of inherent collaboration and overlap between the institutional teams at each level of the work will help the collaborators succeed.
“By aligning our research efforts, we can collaboratively evaluate different materials, catalysts and membranes in order to push this promising technology forward,” said Jiao. “If everything works nicely, I think we will see some early-stage commercialization in the next five years.”
LSU brings strength in catalyst and membrane materials and in engaging chemical companies, such as ExxonMobil, Shell and Dow, and industry partners to the project.
“Chemical manufacturing in the United States is a very big deal. I think we should be thinking about the future,” said Flake. “We already have the infrastructure (pipelines and plants to make derivatives from ethylene) … so we have a huge advantage over the rest of the world.”
The UD and LSU collaborators also want to improve the educational infrastructure around sustainable chemistry to support the chemical manufacturing industry with a trained future workforce. As part of this effort, the team plans to directly involve over 70 undergraduate and graduate students in the project and create opportunities for the students to interact with industry representatives from chemical manufacturers, such as Shell, Dow and ExxonMobil. Other planned activities include engaging K-12 students in Delaware and Louisiana in STEM-related education and career-readiness activities to excite students about the potential of sustainable chemistry.
Contact Us
Have a UDaily story idea?
Contact us at ocm@udel.edu
Members of the press
Contact us at 302-831-NEWS or visit the Media Relations website