
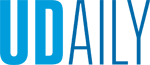

Designs for the real world
Photos courtesy of Cameron Jones and Ashlyn Kapinski February 02, 2022
Senior engineering students team up to solve industry problems
Helping children with disabilities complete everyday tasks that many of us take for granted — like picking up a water bottle or throwing on a backpack — was an effort University of Delaware biomedical engineering senior and Honors student Cameron Jones knew he could get behind.
Jones didn’t hesitate to sign up during the fall semester to be on the team tasked with creating an affordable, 3D-printed prosthetic for children born with upper limb congenital disorders. Not only are high-end prosthetics extremely expensive and often not covered by insurance, but because kids grow so quickly, they have to be replaced or resized every few years. It’s simply not possible for many families to spend the tens of thousands of dollars every few years on a new prosthetic.
“It’s no fault of the kids, parents or families that they’re in this situation,” Jones said. “This is a great project to help the kids have a little more functionality. Why not just help the kids out?”
From 3D prosthetics to automating food packaging operations to optimizing aircraft engines, 224 senior engineering students from the College of Engineering, including Jones, had the opportunity to work with big-name companies and philanthropic organizations on real-world problems during the fall 2021 Capstone Design Program. The students represented the College’s Departments of Biomedical Engineering, Civil and Environmental Engineering, Electrical and Computer Engineering and Mechanical Engineering, with the majority coming from the biomedical and mechanical disciplines.
At the beginning of the fall semester, Jones and three of his classmates teamed up and chose, from over 50 challenges, the project proposed by the MORE Foundation, an Arizona-based nonprofit whose mission is to empower individuals to “Keep Life in Motion '' through innovative research, community education and charitable assistance.
While the students’ creation may not be as high-tech as expensive prosthetics that include electrical and sensing systems, it offers families who had to go without any assistance an affordable solution to make their children’s lives just a bit better.
But it wasn’t easy work making a 3D-printed prosthetic with bendable knuckles, an opposable thumb and compressible fingertips. The trial-and-error process students explored ultimately led to a prototype that may enable a young person the ability to pick up something like a toy, a spoon or a water bottle for the first time in their lives.
“Even in our final prototype, there are things we want to improve on,” Jones said. “But that’s the iterative process of engineering: you just have to keep redesigning and keep building.”
In mid-December, about four months after accepting their engineering design challenge, Jones’s team and 51 others showcased their projects at the culmination of this six-credit interdisciplinary course. Since the program started in 1999, over 500 design challenges have been tackled by 2,000 engineering students working with 100 industry, academic and community sponsors. This time, sponsors included Stanley Black & Decker, Under Armour and Christiana Care, just to name a few.
Many sponsors are looking to upgrade or expand existing products or technologies in new ways to make consumers’ lives easier or safer. For example, the Maryland-based tool and hardware manufacturer Stanley Black & Decker challenged mechanical engineering students to come up with a new dual floor cleaning solution that would allow for mopping and vacuuming within one tool.
“This interdisciplinary program bridges the gap between theory and practice, and it prepares the students well for what lies ahead after graduation,” said Ashutosh Khandha, assistant professor in the Department of Biomedical Engineering.
Pandemic problems
COVID-19 has posed unprecedented challenges for most industries, and companies are looking for innovative ways to address their unique problems. In the case of W.L. Gore & Associates, company officials wanted to showcase how well its N95 mask performs against its competitors.
Not only would their project have to interactively display how the mask works, and do so safely, but it would also have to be aesthetically pleasing since it would be on display for anyone passing through the Gore Capabilities Center in Newark, Delaware.
Working on a project related to the pandemic was important to mechanical engineering senior Clare Dudley, who said her family has been hard hit by COVID-19.
“This is something we built that a big company like Gore is going to use and hearing them say they liked it was really cool,” Dudley said.
Now, as these students head to graduate school, industry or elsewhere, they’ll be able to say their design is on display for a well-known international company. Khandha said about two-thirds of UD engineering students pursue industry careers after graduation, so facing a challenge on a tight timeline (the months-long semester) prepares them for the real world.
In addition to the devastation and problems the pandemic has caused, the expanded use of virtual meeting formats has also made it easier than ever to connect across continents and time zones. While a return to campus this fall revived the hands-on, in-person elements of the program, 2021 also marked the first time an international sponsor participated in the Capstone Design Program.
The University of Cape Town in South Africa proposed three interdisciplinary engineering projects, including one that could have a significantly positive impact on low-income families struggling with a surprisingly common medical condition.
Around the world, a variety of diseases can lead to anorectal malformations that can be life-threatening and often require surgery, devoted at-home care and follow-up procedures. In South Africa, a severe wealth disparity means that some families are unable to afford the devices needed to help a child recover from anoplasty, a procedure that involves reconstruction of the anus.
“When people don’t have really good access to dilators, they use household objects,” said faculty adviser Julie Karand, explaining the importance of the University of Cape Town’s effort to find an alternative take-home dilator for communities in South Africa. The device UD students aimed to create was a more affordable and user-friendly version of the dilator kits hospitals would normally give to patients.
They were able to create a safe, plastic-based product that comes as one unit with exchangeable extensions that are different sizes, instead of a package of separate pieces. The students worked with medical professionals to get the sizing correct and ended up with a product that costs less than $6 to make, which is a fraction of the cost of the hospital-issued devices.
Not only did they find a cheaper solution, but their design will also be universally available since it can be 3D-printed. The open-source nature of their results was a requirement of the project proposed by the University of Cape Town.
“We’re trying to provide access to this medical device for everyone,” said biomedical engineering senior Tori Reiner, one of the students on the five-student team that tackled this project. “This project opened my eyes and allowed me to put my foot in the door to start working on something significant like this to make the world a better and healthier place.”
Lessons learned
While many of the teams were able to successfully engineer assigned challenges into new and improved solutions, every year there are a few problems posed that cannot be solved in just a matter of months. And over the years, it seems that the challenges have become more and more complicated, said Khandha.
“We also have a lot more industry focused projects compared to previous years,” he said, noting that despite the increasing level of challenge, students have still been able to succeed year after year.
From understanding the problem to evaluating multiple solutions to finally designing and creating an end-product, UD’s Capstone Design Program aims to give students the time-constrained, interdisciplinary experiences they’re sure to encounter after graduation.
The project even inspired Jones’ teammate, Ashlyn Kapinski, an Honors biomedical engineering senior, to create a children’s book on how to use and care for the 3D-printed prosthetic hand.

“This project has meant so much to me in addition to re-designing the prosthetic hand,” Kapinski said. “I think educating children on how to use their device is crucial to ensuring their safety and avoiding frustration. User guides are usually too dense and technical for a child to understand, and I hope that by providing a guide in a picture-book format, we can better get the right message across in a fun way.”
While many teams end the semester with a final product, not having a perfect prototype in hand after just a few months isn’t necessarily seen as a failure. In such cases, the projects can continue as independent study the next semester, or the project may return for the next group of senior engineering students to tackle, Khandha said. Even for teams who did finalize their project, these blossoming engineers may still have ideas for further improvements, as is the case with Kapinski and Jones’ team’s 3D prosthetic, for example.
“Engineers are at the interface of technology and human needs,” Khandha said. “Being able to be productive with limited resources in face of the challenges that we cannot anticipate, like COVID, and still having the fundamental engineering skills to be independent and conduct the required work, that’s a big deal.”
To see all the 2021 senior design projects, including 90-second videos produced by each of the 52 teams, go to engr.udel.edu/senior-design-celebration.
Contact Us
Have a UDaily story idea?
Contact us at ocm@udel.edu
Members of the press
Contact us at 302-831-NEWS or visit the Media Relations website