
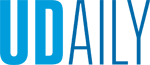
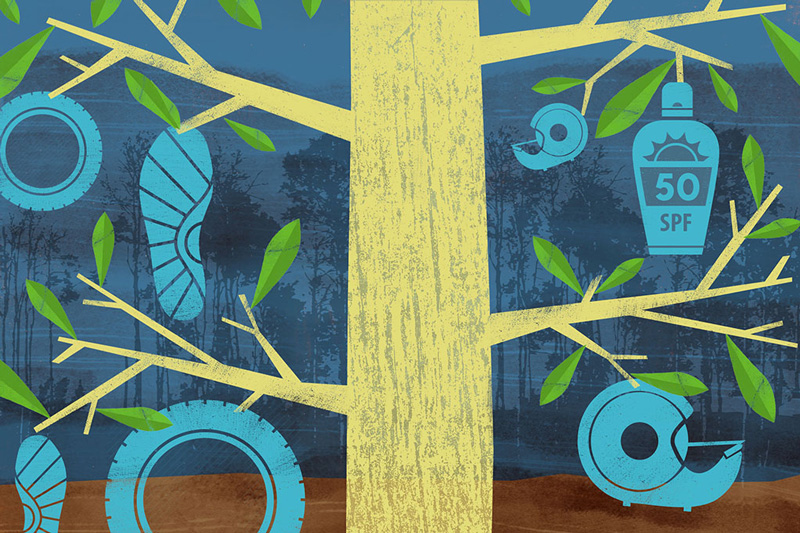
Cracking the code
Illustration by Jeffrey Chase February 12, 2020
UD researchers explore methods to turn biomass into sunscreens, shoe soles and more
Lignin is a major waste product of the pulp and paper industry that can be converted into chemical building blocks to create other materials. It comes from trees, grasses and other biomass.
Over 70 million tons of lignin is left over annually as a byproduct of pulp and paper manufacturing processes. Biorefineries and paper manufacturers currently burn lignin for heat or discard it in landfills. This inefficient use of a potentially valuable raw material is a massive economic, environmental and societal stressor that needs a renewable solution.
With a $3.69 million grant from the National Science Foundation, University of Delaware’s Thomas H. Epps, III and an interdisciplinary team of experts will unlock new routes to sustainably develop materials from lignin. The funding is part of a broader NSF effort to support research driven by specific and compelling problems, in this case materials life cycle management, which includes everything from how materials are developed and created to how they are disposed of at the end of their useful life. The UD work is among the first cohort of awards in the new Growing Convergence Research initiative — one of NSF’s 10 Big Ideas.
Epps, the Thomas and Kipp Gutshall Professor of Chemical and Biomolecular Engineering at UD, is the project’s principal investigator. He has assembled a team of researchers with expertise in catalysis, polymer chemistry, polymer engineering, environmental toxicity and ecohydrology to tackle this problem.
The research team aims to develop and evaluate comprehensive strategies to convert lignin into more valuable products, such as lubricants, sunscreens and adhesives, or impact-resistant materials, from rubber bands, gaskets and shoe soles to car tires, dashboards or bumpers.
The project leverages UD's institutional strengths in catalysis, energy and polymeric materials, and it involves faculty from three of UD’s eight colleges: the College of Engineering, the College of Earth, Ocean and Environment and the College of Agriculture and Natural Resources.
Major faculty participants and co-principal investigators (PI) on the project include Dion Vlachos, director of the Delaware Energy Institute and the Catalysis Center for Energy Innovation, and the Allan and Myra Ferguson Professor of Chemical and Biomolecular Engineering; Delphis Levia, professor of ecohydrology and chair of geography; Aditya Kunjapur, assistant professor of chemical and biomolecular engineering; Changqing Wu, associate professor of food toxicology; and LaShanda Korley, Distinguished Associate Professor of Materials Science and Engineering.
Recyclable, friendly materials
One major challenge is that lignin traditionally is the hardest part of the biomass to break down. Additionally, different kinds of biomass (trees, grasses) have different chemistries, which can influence the types of molecules and materials that can be generated from the lignin.
The researchers plan to develop a roadmap that links environmental factors, such as where the biomass comes from and how it grows, to how the end products created from the biomass perform, while also considering the downstream impacts of biomass use.
“One of the big problems that we want to address is sustainability,” said Epps, who also holds a joint appointment in materials science and engineering and directs the Center for Research in Soft Matter and Polymers at UD. “Not just thinking about whether we can make new polymers or catalysts from biomass, but understanding the impact of these polymers on the environment, in terms of toxicity and in terms of the resources.”
An exploratory aspect of the work involves looking at whether these molecules can be broken down into their original components after their useful life is over. Epps explained that when polymer materials are reused, the new material’s properties, such as strength or flexibility, are normally not as robust as the original polymer. A material’s performance typically degrades each time it is reprocessed.
Instead, the UD research team is exploring ways to break materials back into their chemical building blocks so that they can be regenerated in a way that retains the full properties of the original material.
“This regeneration would make things that are infinitely recyclable,” Epps said. “If we could break polymer materials back into their monomer building blocks, we would have a blank slate. We could build the exact same thing or maybe something even better.”
Each member of the research team brings knowledge and experience critical to driving forward sustainable materials development. For example, Vlachos’ extensive expertise in catalysis — processes that accelerate chemical reactions — lends itself nicely to creating the molecules that Epps and others need to make polymer materials. Similarly, Epps’ monomers and polymer designs can help Korley develop polymer networks with specific mechanical properties, like toughness. These skills, Epps said, can help other scientists and engineers turn polymers and other materials into functional items like toy action figures or airplane wings.
Meanwhile, Levia’s hydrology and forest ecology know-how can help the research team explore noninvasive methods to predict the chemistry in trees so that they can design ways to make materials from biomass that are not only better, but also environmentally friendly and nontoxic. Wu can lend a hand here, too, by providing the research team with information about how different structures lead to more or less toxicity in materials, which can inform Kunjapur’s work engineering different enzymes and organisms to make specific molecules.
Six graduate students from across the project’s three collaborating colleges will work as an integrated team to link stem flow chemistry in forests to the structural properties (strength, impact resistance) that the researchers are finding in polymers being developed out of the biomass.
“This interdisciplinary work has potential to drive forward a circular economy that eliminates waste and encourages the continued reuse of resources. UD can be a leader in this area,” said Dion Vlachos, director of the Delaware Energy Institute and a co-PI on the project.
Contact Us
Have a UDaily story idea?
Contact us at ocm@udel.edu
Members of the press
Contact us at 302-831-NEWS or visit the Media Relations website